Powder Coating Durability
The durability of powder coating depends on a number of factors including the types of pretreatment, powder, metal coated, the design and fabrication of the product and environment where the product is in use.
-
Pretreatment : This is the process used to prepare the metal surface before coating to remove mill finish, dirt/debris, oils, contaminants and to provide the best adhesion of the coating to bond the powder to the metal surface. Processes such as media blasting, primer, preheating and chemical pretreatments can be used. This step is a critical factor in the powder coatings durability and also plays a large role in cost factoring.
-
Powder : Not all powder coating material is the same. There are a number of different types of powders such as epoxy, urethane, polyester, hybrid, TGIC, TGIC-free, Acrylic, fluoropolymer and many more. Each of these types of powder are used based on the customers needs such impact resistance, UV protection and others. Each comes with different durability ratings.
-
Metal Type : The type of metal being coated is a significant factor in durability. Aluminum coated with a fluoropolymer powder can have an expected durability of 20 years* while steel coated with a polyester powder can have a durability expectation of 1 year depending on the type of powder and environment where the product is located.
-
Design & Fabrication : How a product is designed and fabricated plays an important role in durability. Powder coating can only be applied to the exterior surfaces of a product. The surface where two metals are welded together and on top of each other cannot be coated because it cannot be accessed by the powder. However, environmental conditions such as humidity and water will penetrate that area over time and corroding. This can cause "rust" to run down the outside of the part. The appearance of rust does not indicate a failure in the coating and can usually be removed with a light application of
Advantages of Powder Coatings
Powder coating is the preferred choice for finishing for manufacturers and consumers alike. Along with its attractiveness, powder coating’s baked on finish offers several advantages over its competitors, including:
-
Harder product increases durability against nicks and scratches
-
High-quality finish maintains color longer with less fading
-
Resistance to corrosion
-
More environmentally friendly
-
Typically less expensive
Powder coatings also don’t emit any VOCs (Volatile Organic Compounds). VOCs are by-products of a number of chemical compounds, including paints and other surface coating techniques, and are emitted as gases into the indoor and outdoor environment. Powder coating produces less hazardous waste than liquid coatings, which makes it more sustainable and ecological sound.
Disadvantages of Powder Coatings
The disadvantage of powder coating comes when it needs to be repaired. Though it has increased durability it is not as easily fixed in the event that it is damaged or wears. For that reason it is best to maintain any areas where the outer surface is damaged immediately. Liquid paint and powder coating both require regular inspection and maintenance. The following is the best recommendations to keep your finish lasting.
Factors that effect the longevity of the finish
The service life of an powder coating cannot accurately be predicted due to the number of variables that can affect its ability to beautify and protect the surface where they have been applied.
Professional finishing company have difficulty giving a firm answer to any of the following:
-
How long a particular finish will last
-
The rate at which the coating will start to lose either its protective or decorative value
-
The rate at which values are lost
These are impossible to predict with any degree of certainty. A definitive answer is likely overreaching due to the variability of use and environment.
Aside from physical abrasion elements that can affect your powder coating finish include:
-
Geographical location of the building
-
Environment surrounding the building e.g. marine, industrial, alkaline or acidic, etc.
-
Levels of atmospheric or applied pollution including rock salt
-
Exposure to sun, rain, cold and freezing temperatures, electrical currents , prevailing winds and the possibility of air borne debris causing erosive wear of the coating e.g. sand causing abrasion or particles along a road
-
Protection of part or all of the building by other buildings
-
Change in environmental circumstances during the lifetime of the building e.g. if rural became industrial
Powder coatings that are applied to metal products exposed to the weather will inevitably degrade over time. A number of conditions, including those found in nature, will contribute to shortening the life of this type of protective finish by causing it to break down.
The right type of care and maintenance is essential to combat the detrimental effects of the elements . No powder coating is entirely maintenance-free — over time, it will lose some (or all) of its decorative and protective properties due to the effects of weather and other influences. While it may not be possible to map out the exact length of service life you can expect to get from fabricated products, you can extend their effective service life with the right cleaning and maintenance. It could double or even triple the coating’s effective service life.
How to Maintain Exterior Powder Coated Surfaces
The more value you attach to it, the more important it is to invest in regular maintenance efforts. Maintaining the good looks of your powder coated products is just like caring for your car – and is a smart way to protect your investment. Over time with exposure to the elements, powder coatings may show signs of weathering such as loss of gloss, chalking and slight color change. A simple regular clean will minimize the effects of weathering and will remove dirt, grime and other build-up detrimental to all powder coatings.
The frequency of cleaning depends in part on the standard of appearance that is required and also the requirements to remove deposits. In most cases, the cleaning of powder coated sections can be conveniently carried out at the same time as window cleaning. However, the recommended frequency of such cleaning will depend on your specific needs:
Non-hazardous Environment | Clean and check every 12 months
Tropical Environment | Clean and check every 9 months
High Traffic and Swimming & Leisure Pools | Clean and check every 6 months
Marine Environment | Clean and check every 3 months
Industrial Environment | Clean and check every 3 months
WARNING Avoid Harsh Chemical Cleaners. Powder coatings are damaged by harsh solvents. A number of commercial cleaning products can cause damage to these types of finishes. Once the finish has become damaged, it is much more vulnerable to fading, staining and failure of the finish itself. When harsh chemical cleaners are used on powder coated surfaces, the life expectancy of the finish can reasonably be halved.
Tips for Caring for Exterior Powder Coated Fences, Railings and Gates
Inspection and Cleaning. Powder coated should be inspected at least yearly and preferably every six months. To inspect the railing simply purposefully observe all the surface of the finish. During your inspection look for damage, scratches, or nicks and inspect for signs of rusting. Tighten or replace any loose or missing parts immediately. Evaluate the needs to removed build up and be cleaned. If the iron work is placed in a high-traffic area or where exposed to salt, the inspection should be performed more often.
Powder coating is a very durable finish, but requires maintenance. When dirt and grime builds up in the joints and crevices of fences, railings, and gates, it can create a place where bacteria gather and insects find a home. Both circumstances only serve to speed up the breakdown of the coating.
Where salt is applied to stairs and walkways or in coast areas, salt water can damage railings, fences, and gates. If they are not thoroughly cleaned at least once a year to remove the buildup, salt will remain attached to the coating and dull its appearance, leaving it looking chalky and damage the finish. To extend the life of your iron work you’ll need to make sure you clean it properly.
-
Start by wiping the surface gently with a wet sponge to remove any loose dirt and debris. You can also use a soft brush for this purpose. A wire brush would be too harsh, since it would damage the finish. Your goal is to remove most of the surface dirt and dust at this point.
-
To remove salt and any other deposits from the surface of the fence, railings, and gate, use a soft brush and a mild household detergent.
-
Choose a detergent that is free from both solvents and petroleum-based chemicals when cleaning your powder-coated fence. One way to tell whether the detergent you are considering is safe for a powder-coated surface is whether the product is safe for your hands. If you need to protect your skin by wearing gloves when using the product, it’s probably not safe for the surface of the gate, either.
-
Rinse the detergent off the fence or the gate using lukewarm water. At this point, you can allow it to either dry naturally or use a clean, dry cloth to dry it off if you would like to get a cleaner look.
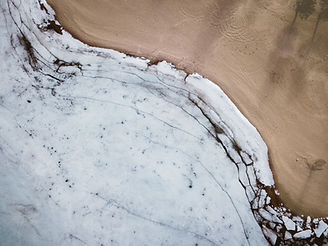
Get in Touch
This is a Paragraph. Click on "Edit Text" or double click on the text box to start editing the content.